In part one of this series, we focused on batt-type insulation as well as two knit active insulations. We covered how these insulations are manufactured, their benefits and drawbacks. We covered issues related to how the insulating value of the insulations are measured by the industry. We presented the results of our measurements of thermal resistance for 11 insulation products.
In part two, we looked at fleece insulation. We learned that:
- Fleece is not very warm.
- Fleece is heavy for its insulating value.
- Despite our expectations to the contrary, fleece weight seems to have nothing to do with warmth.
In this article, we will focus on an important claim on which synthetic insulation has based a large portion of its competition with its main alternative – down. That issue is whether synthetic insulation will really keep you warm when it is wet.
I will start out by saying that I expect anyone who has worked up a good sweat while wearing their synthetic insulated jacket and then taken a break may already know the answer to this question. I have experienced that chill and have always wondered why manufacturers (or at least some) make the claim warm when wet when describing their products. This article demonstrates that synthetic insulation will not keep you warm when it is wet! Perhaps when it is damp, but not when it is wet.
Why do we get cold if our insulation gets wet?
Let’s start with a fundamental concept. We all know that insulation works by trapping air. The spaces between the fibers in synthetic insulation accounts for more than 90% of the volume in of your typical batt. That is where the bulk of resistance to losing heat from your body is located. The fibers themselves can have varying amounts of thermal resistance. However, these fibers will always have lower thermal resistance than trapped air.
A batt is a section of non-woven material sandwhiched between two layers of fabrics to provide loft and insulation in garments, sleeping bags, and quilts.
A material’s ability to transfer heat is called thermal conductivity. As thermal conductivity increases, the rate of heat transfer across an object increases for a given temperature difference across that object. The thermal conductivity of water is 23 times greater than the thermal conductivity of air. If you replace all the air in your insulation with water (assuming the insulation could still maintain its volume) over 90% of the insulation would transfer 23 times more heat than dry insulation.
You can estimate the best and worst case for thermal degradation of soaked insulation. The best case, if the insulation collapses and all water is drained out (unlikely) is that heat loss doubles. The worst case, if all air spaces fill with water but the insulation retains its structure (really unlikely) is 20 times more heat loss. In either extreme, you will probably be pretty unhappy.
In reality, neither extreme will happen. The water accumulation in your insulation will never replace all the air because at some point, water will begin to drain out or the insulation will collapse from the weight of the water.
Face fabrics and inner fabrics that are designed to resist the entry of liquid water may still have limited ability to restrict the entry of water vapor. Sweat from your body evaporates and becomes water vapor. The water vapor will then penetrate the fabric of your insulated garment as it tries to travel out to the ambient. As the vapor moves into the insulation, away from the body, it may eventually encounter temperatures at or below the dew point. At this location, the vapor will condense and deposit liquid water inside the insulation. Even if you shield your insulation from rain, it may still become wet due to condensation of vaporized sweat.
This wetting process is never a foregone conclusion. It will be influenced by your level of activity, ambient temperature and humidity conditions, the ability to provide ventilation in your layering, and the MVTR (moisture vapor transmission rate) of your layers.
What does the industry claim about warmth when wet?
I don’t know if Andrew Skurka would consider himself part of the industry, but here is his take on the issue: “In specific regard to the issue of moisture sensitivity, I want to point out that synthetic insulations are absolutely not ‘warm when wet’ like is often claimed.”
What does Primaloft have to say about its various insulations? It actually provides clo/ounce values for wet and dry insulations in its product specification sheets. Table 1 provides their data for some of Primaloft’s products.
Table One: Claimed Wet/Dry Clo/oz.yd2 Values for Primaloft Products
Insulation | Clo/oz/yd2 Dry | Clo/oz/yd2 Wet | % Loss Wet |
---|---|---|---|
Silver | 0.79 | 0.72 | 8.9% |
Gold | 0.92 | 0.9 | 2.2% |
Gold Eco | 0.92 | 0.9 | 2.2% |
Gold Active | 0.81 | 0.67 | 17.3% |
According to Primaloft, the loss of thermal performance due to wet insulation ranges from negligible to small. Primaloft cites ISO 11092 for the testing methodology used to produce these numbers. ISO 11092 provides no guidance for testing thermal resistance of wet fabrics. Nor does it provide guidance for producing clo value data to describe thermal performance. As we will discuss below, measuring the performance of wet insulation is complex and we have no idea how they derived their claims.
A substantial shortcoming with the Primaloft data is that it does not specify what is meant by wet. Obviously, wetness varies from a few trapped molecules of water to complete saturation. The level of wetting in an insulation will impact its thermal effectiveness as the amount of trapped air is replaced by increasing amounts of liquid water. One way to measure the amount of wetting in insulation is to weigh a dry insulation sample and then reweigh as water is added to the sample. The level of wetting may be expressed as a percentage of dry weight. If an insulation sample weighs 25 grams and 25 grams of water are added, then the wetting level is 100%.
3M Thinsulate states the following in their specifications: “Warmth While Damp –Retains most of its insulating ability even under damp conditions. Individual fibers absorb less than 1% by weight of water. Easily dried.” By comparison with Primaloft, 3M qualifies wetness as damp. The amount of water trapped in the insulation is not specified. The impact on warmth is not quantified. The description is more nuanced than the approach taken by Primaloft, but still a very weak claim.
Climashield says the following about its Apex and other insulations: “Warmth When Wet – Maintains warmth, even when wet, without impeding moisture permeability. Prevents a ‘clammy’ feel during use.” Climashield, as far as I can find, makes no quantified claims about wetting level or how much thermal performance is lost when making these statements.
Polartec, in the literature that we have access to, makes no claims about warmth when wet in their various insulating products. They simply claim that the products dry quickly when wet.
How can warmth when wet be measured?
This is a challenge.
The basic method of measuring thermal resistance is fairly straightforward.
- Measure the temperature on the top and bottom of the object under test.
- Measure the amount of heat energy that flows through the test object to maintain consistent temperatures on top and bottom.
- Divide the result of step one by the result of step two.
In order to measure thermal resistance accurately, steady-state heat flow must be established across the test subject. That means that the temperature at the bottom and top of the test object is constant. The heat input to the test object is constant. If any of these measured quantities are not constant, the calculated thermal resistance will be incorrect.
If we try to measure the thermal resistance of a piece of wet insulation, we need to apply heat. Once the heat is applied, the water in the test sample will start to evaporate. As evaporation occurs, some of the heat that is being added will be consumed when turning liquid water into vapor as evaporation occurs. This extra amount of heat has nothing to do with the R-value measurement but cannot be removed from the measured heat input. As the test continues, and evaporation continues, the water contained in the test sample will diminish, the effective thermal resistance of the sample will steadily increase. The amount of heat delivered for the test to maintain constant top and bottom temperatures will then decrease. Throughout this process, the amount of heat energy input to the wet test fabric will constantly change.
The method that I developed for this test attempts to provide a steady-state condition.
The test method is designed to simulate vapor introduced into a garment by sweating.
The permeation kettles that I use to measure thermal resistance are filled with water that is kept at a temperature maintained by the kettle controls. The kettles are sealed with an impermeable plastic membrane that also provides a work surface. The temperature of the work surface is monitored by a thermocouple array. For this test, the impermeable plastic membrane is replaced with a metal grid. A thermocouple is mounted at the center of the grid to provide a temperature measurement of the bottom of the test sample. The test sample is set on the grid. In this configuration, vapor from the hot water in the kettle can flow continuously into the insulation test sample. The picture below (Figure 1) shows the grids mounted on the kettles.
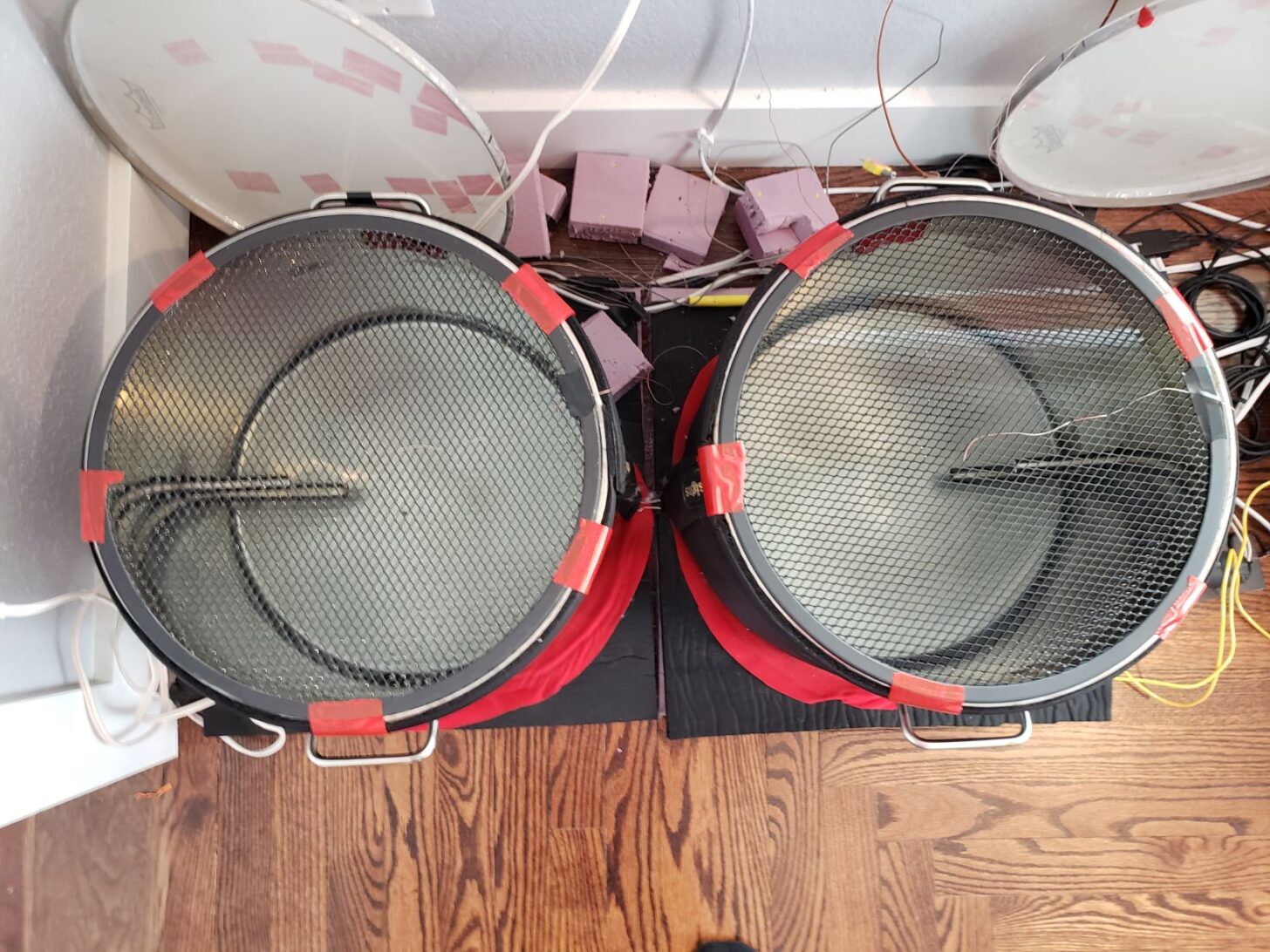
This configuration permits heat and vapor to be supplied to the test insulation at a steady rate.
Ryan Hannigan of RBH Designs (RBH Designs manufactures vapor barrier clothing) produced four insulation pillows for the test. Two contain 6 osy (ounce per square yard) Primaloft Gold. The other two contain 6 osy Climashield Apex. For each set, the bottom fabric of one pillow is made from 2 ply Vaprthrm fabric, a proprietary vapor barrier fabric utilized by RBH Designs. This fabric prevents vapor from entering the control pillow, which is always placed on the left kettle. The top fabric of each pillow pair and the bottom fabric of the right pillow is a 1.1 oz ripstop nylon, uncalendared and uncoated, from Ripstop by the Roll. The below photo (Figure 2) shows the pillows mounted on the kettles.
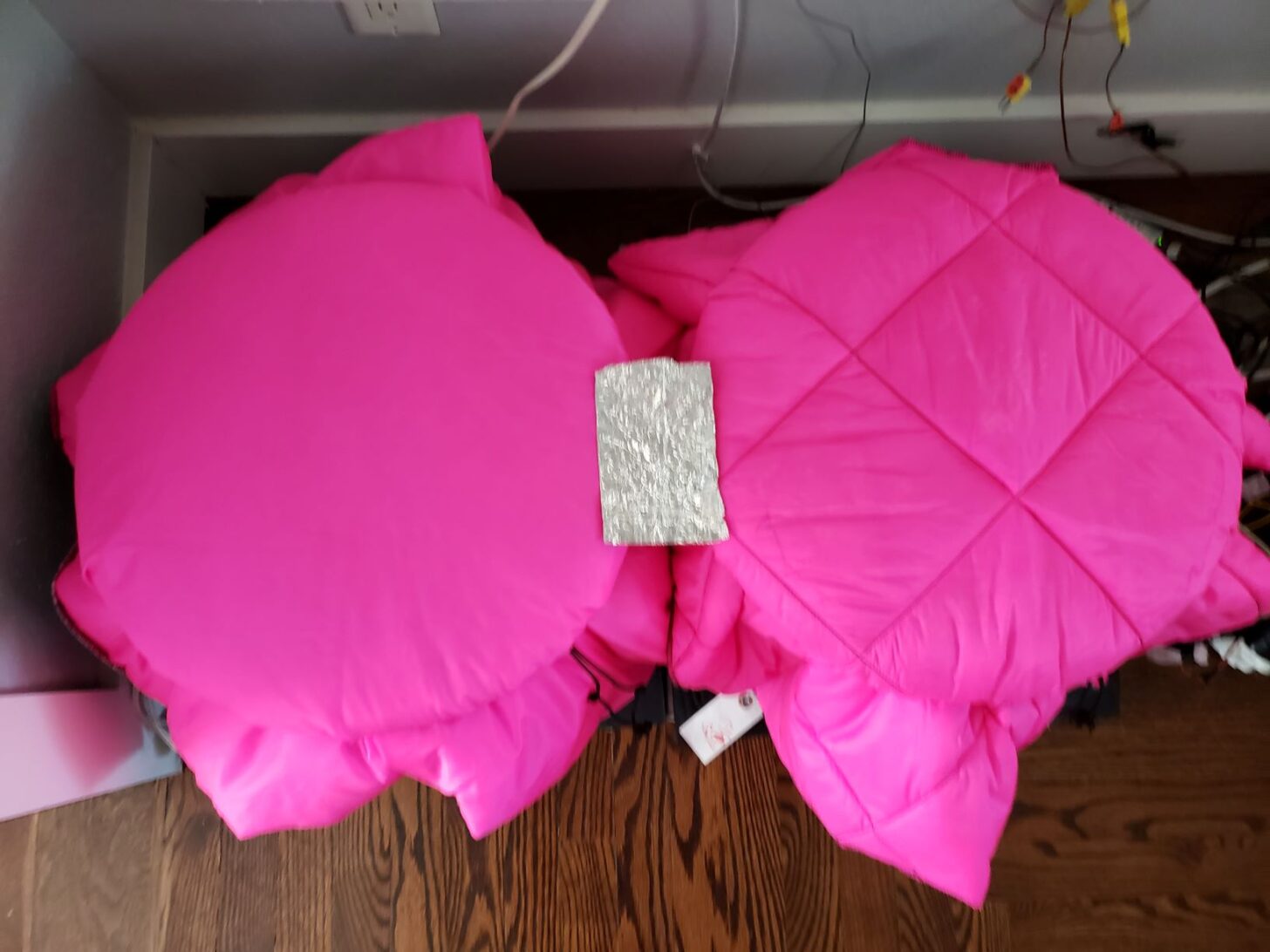
When the test is conducted, the left pillow will produce R-value measurements that show the performance of dry insulation. The right pillow will show the performance of wet insulation.
The key to this test method is achieving condensation inside the pillows. This was accomplished by manipulating the kettle water temperature and the room temperature until evidence of condensation was identified in the infrared image of the two kettles. The initial test was conducted with a kettle water temperature of 100 °F (38 °C) and a room temperature of 70 °F (21 °C). With this configuration, the vapor passed through the right pillow and produced no temperature change on the pillow surface and no relative change of surface temperature between the two pillows. No condensation was occurring. At a water temperature of 140 °F (60 °C) and a room temperature of 50 °F (10 °C), a significant temperature difference developed between the two pillows. Condensation was occurring in the right pillow.
The test was performed as follows:
- The pillows were weighed.
- The pillows sat on the kettles for an initial 30 minute period to warm up and reach steady state. Steady-state was achieved when the top surface temperatures were stable.
- A thermal image was acquired at 30-minute intervals over a two-hour period. When each image was produced, the R-value for each pillow was measured.
- At the end of the test, the pillows were weighed to calculate the amount of water trapped in the pillows.
Test Results
Figure 3 shows the thermal image of the Primaloft pillows used to calculate R-value at a water temperature of 100 °F (38 °C) and an ambient of 70 °F (21 °C). Figure 4 shows the thermal image of the Primaloft pillows at a water temperature of 140 °F (60 C°) and an ambient of 50 °F (10 C°).
Member Exclusive
A Premium or Unlimited Membership* is required to view the rest of this article.
* A Basic Membership is required to view Member Q&A events
Home › Forums › By the Numbers: Is Synthetic Insulation Warm When Wet?