TL;DR
I made a 6400 ci / 105 L pack out of repurposed car airbags, with a frame made from a baby carrier. The packbag weighs 19.5 oz / 553 g and with the suspension system included weighs 44.75 oz / 1269 g.
Here are a few photos of the finished pack:
Background
In this thread, I wrote about my last upcycled backpack, made from an old porch umbrella with a frame made from a cut-down baby carrier. I loved using that pack; it was supremely comfortable and I could fit anything in it from winter trips to family gear.
Unfortunately, the umbrella fabric proved to not be durable – apparently having been out in the sun and weather day after day for years made it brittle. When it ripped, it did so spectacularly. On a winter trip, one of the side pockets ripped clean off.
I started to get holes all over the bag, especially at abrasion points and patched them with more and more duct and Gorilla tape. It made it through eight short trips before becoming unserviceable. But that’s OK; I had expected it to be a prototype for this project using car airbags as the pack fabric.

Several years ago, I read an article about Ursacks on the Section Hiker website, and in the comments section, Ken “DripDry” Holder shared about making a bear bag out of an airbag. This was based on the idea that airbags are meant to be extremely tough and lightweight – like the Ursack’s fully woven UHMWPE – but are much cheaper (or even free) when repurposed from old vehicles.
DripDry ended up writing a full how-to article on Gossamer Gear’s blog about this a couple of years later. I became very excited by the idea of building a backpack out of this material. One of my good friend’s uncles owns an auto body shop, and he started to cut airbags out of junkers for me until he had a whole bag full.
A few years ago, I found a guy on Craigslist an hour from me selling his Kelty White Cloud made of fully woven UHMWPE (Spectra) and I went to go check it out. While I’m not equating them, the look and feel of the two fabrics were very similar, even though airbags are typically made of woven nylon.
At home, I performed non-scientific durability tests on the airbag fabric and was quite pleased with the results. I could hammer a nail through the fabric into a piece of wood and then was unable to tear the fabric by pulling it against the nail. If I make a cut, I’m unable to tear it further with my hands. I scraped it hard 42 times in the same place with a sharp rock before it finally cut through the material.
In my online research, I found several examples of airbag backpacks, but they were all upcycled fashion items, none made for backpacking or heavy use. I drew up a bunch of possible designs but ended up going with one heavily inspired by Dave Chenault’s commentary about the future of ultralight packs and Luke Schmidt’s DIY ultralight backpack article, as I had with my previous pack, knowing that the design worked extremely well for me. The cut-down baby carrier from that pack serves as the frame for this one. I’m so appreciative of both Dave and Luke’s ingenuity and generosity in sharing their designs.

Issues and Notes
I’m looking forward to putting miles on this pack, which will be the real determinant of the fabric’s durability. I’m optimistic about the use of airbags as an ideal backpack material that has that unobtanium trifecta of ultralight, ultradurable, and ultracheap.
However, there are several issues (and workarounds) to be aware of that I discovered along the way.
Coated vs. uncoated
Some airbags are coated with silicone and are waterproof. The ones that aren’t coated just soak up water. Less than half of the bags I received were silicone coated. I tested every airbag I had by putting each one over a glass filled with water with a rubber band around it, then inverting the glass overnight.
Different materials
Since airbags are made by a number of different companies, their composition is different. A few pieces had a really thick and slick layer of silicone on the inside, while others had a much subtler coating (which I prefer). One coated airbag out of the whole bag I received from my friend’s uncle felt like a much cheaper and thinner material and I was able to rip it with my hands. I can’t imagine how that one passes an auto safety test. The only information I have on the fabric is one piece has “420d” printed on it, which may stand for 420 denier, or it may not – there are a bunch of numbers and letters printed on the airbags.
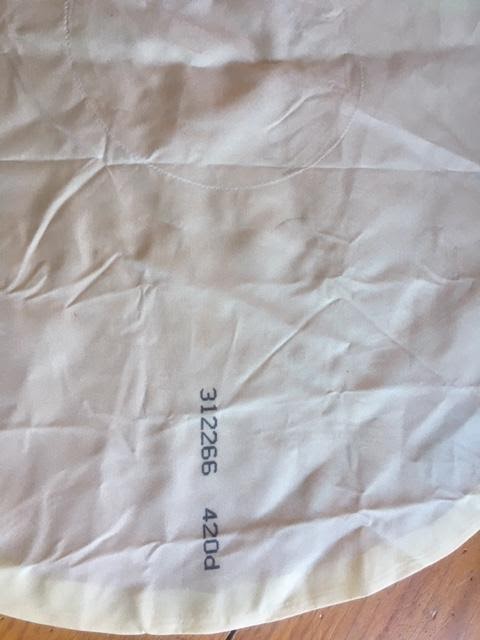
Color
You don’t get to choose. Primarily, the uncoated airbags are white and look cosmetically like fully woven UHMWPE. The coated ones tend to be colors – mostly pink and baby blue; sometimes yellow. My pack uses all of these colors. I tried painting a sample piece gray with many coats of watered-down acrylic paint (a technique I learned here on BPL), but then just decided that the funky colors are part of the charm. I’ve been calling this pack Big Pink, but Rainbow Sherbet might be a more accurate name. Or The Pastel Peakbagger?
Patterning on small pieces
To build this backpack, I spent hours seam-ripping the triple-stitching on circular and oval-shaped airbags, which means there are stitch holes left in weird places that need to be sealed with silicone. Then I had to do some creative patterning and use extra seams to join smaller pieces together. For example, the massive rolltop on this bag uses four pieces of fabric instead of just one.
There are companies that make airbags that have seconds-quality runs (unsuitable for car safety standards) of material yardage. However, I was unable to get these companies to sell me their seconds, especially since I was only looking to buy a few yards. Because of my limited supply, and my desire to not waste the material, I had the airbags for seven years (!) before finally committing a few months ago (once my umbrella pack died) to actually building it.
It’s far from perfect – there are wavy seams, a pucker in one place where the roll-top meets the main body, and I thought I was going to lose my mind trying to get the bottom to line up correctly, but it will be functional and comfortable and for that I’m content. The vertical seams are triple stitched and either flat-felled or bound and felled, and the bottom is triple stitched with grosgrain binding.
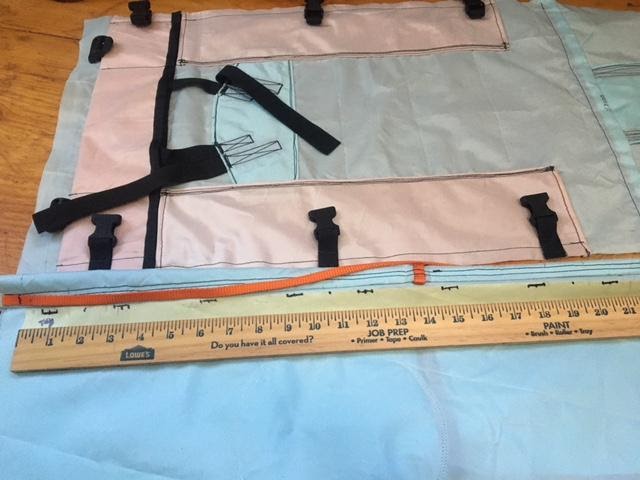
Weight
Oh yeah, the weight! This pack is roughly similar in size to my old Lowe Alpine Contour IV (6400 ci / 105 L). The packbag alone is 19.5 oz / 553 g (not including the shoulder straps, frame, and hipbelt). The total weight of the pack including the suspension elements is 44.75 oz / 1269 g. For winter use, I’ll run it with bottle parkas attached to the hipbelt and a compression panel (which add 8.3 oz / 235 g with long straps and buckles) that I made for my last pack to hold snowshoes. In the future, I’ll add modular side pockets and a top lid and configure the pack with the appropriate accessories for each trip.
Thanks for reading!
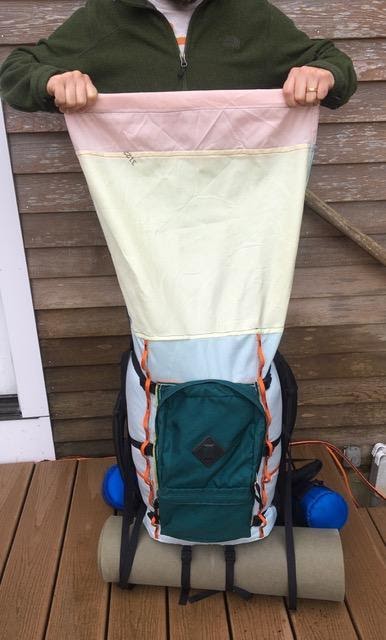
Home › Forums › Ultralight, Ultradurable, Ultracheap: A Backpack Made From Car Airbags